无框力矩电机:人形机器人关节驱动的技术革新与制造挑战
一、技术原理与结构创新
无框力矩电机(Frameless Torque Motor)摒弃了传统电机的外壳、轴承等部件,仅保留核心的转子(永磁体组件)与定子(铜绕组与钢片),通过直接嵌入机械结构实现动力输出。其设计特点包括:
高功率密度:无框结构减少冗余部件,体积缩小30%-50%,扭矩密度提升15%-20%。
低惯量响应:转子惯量低,响应时间短,可支持机器人关节的瞬时爆发力需求(如弹跳、快跑)。
定制化兼容性:支持模块化设计,适配不同关节尺寸(如特斯拉Optimus采用28个无框电机驱动关节)。
技术难点集中于磁路优化与散热设计。例如,德国TQ Robodrive采用20极18槽磁路布局,通过环氧灌封提升散热效率;美国科尔摩根则以12极39槽设计降低转矩脉动,确保运行平稳。
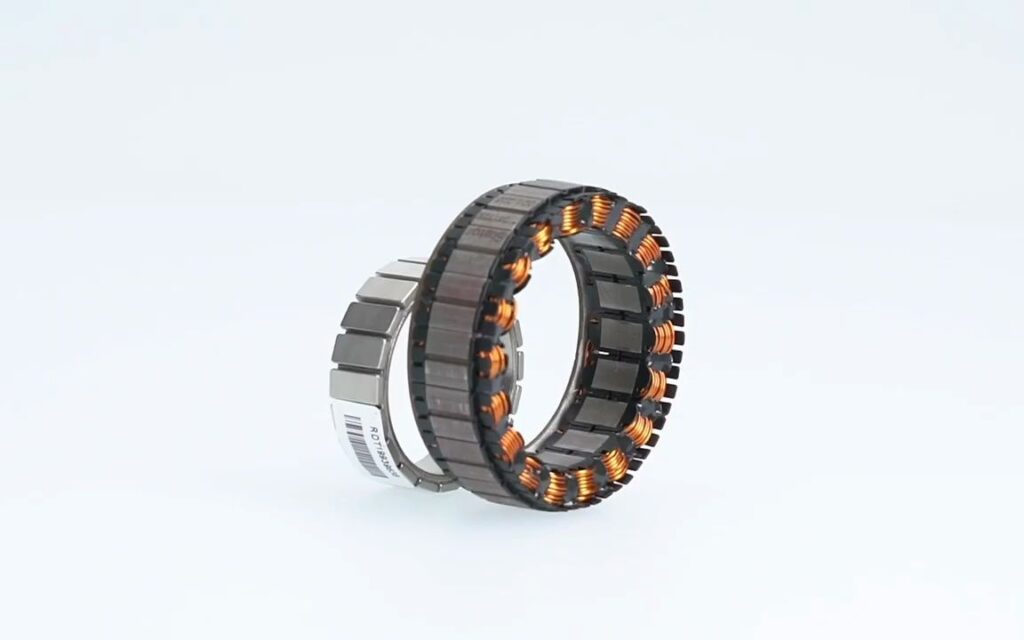
二、应用场景:从工业到仿生的全面渗透
无框力矩电机的核心应用场景已从传统工业机器人扩展至人形机器人、医疗设备等高精度领域:
人形机器人关节:
特斯拉Optimus的28个关节中,无框电机承担旋转与直线驱动,单机价值占比约15.4%。
卧龙电驱的关节模组结合AI技术,可模拟人体运动特性,适应复杂环境下的巡检、救援任务。
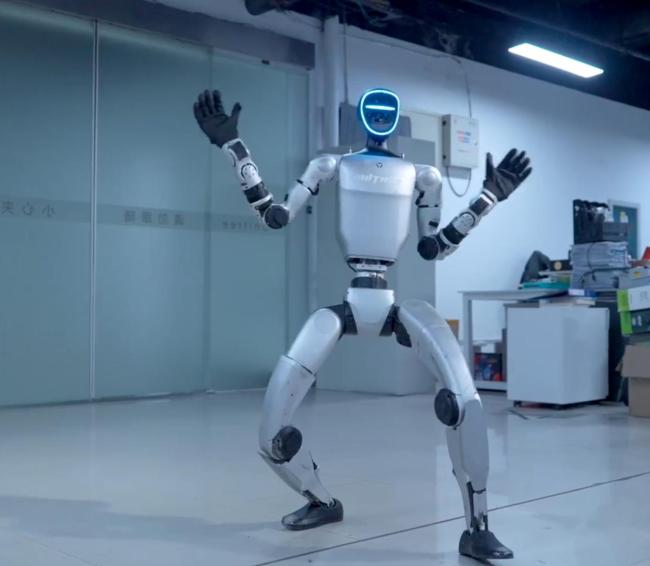
协作机器人:每台协作机器人需6-7个无框电机,其紧凑设计(最小直径25mm)支持高灵活度操作。
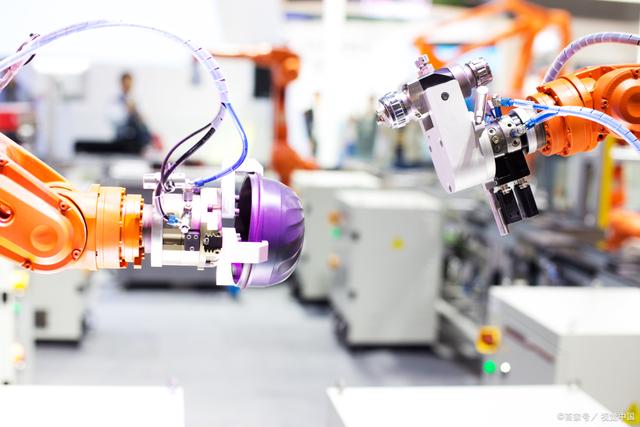
医疗与精密制造:
外科手术机器人中,电机精度可达微米级,支持微创操作;
机床领域,直接驱动技术消除机械传动误差,提升加工重复性。
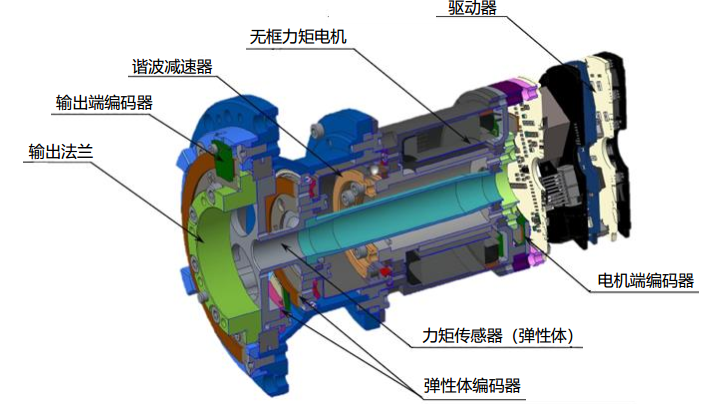
三、制造工艺:精密加工与国产化突破
无框力矩电机的制造涉及高精度机加工与电磁设计,核心环节包括:
材料与设备:
绕线与灌封工艺:
步科股份的第三代产品采用分瓣绕线设计与无框灌封技术,提升散热效率与结构稳定性;
雷赛智能的FM1系列通过优化绕组槽满率,转矩密度较同行高15%。
国产化进展:
步科股份占据国内近50%市场份额,产品外径覆盖52mm-132mm,适配多场景需求;
雷赛智能推出25mm微型电机,2024年进入试产阶段,目标客户包括多家人形机器人企业。
四、竞争格局:外资主导下的国产替代机遇
外资品牌:科尔摩根(美)、TQ Robodrive(德)等占据高端市场,技术优势在于磁路仿真与工艺稳定性。
国内厂商:
步科股份:第三代产品性能对标国际,第四代研发聚焦轻量化与成本优化。
雷赛智能:微型驱动器与人形关节模组进入试销,2024年产能规划明确。
卧龙电驱:联合AI技术开发仿生关节系统,拓展电力、医疗等垂直场景。
市场前景:2025年全球人形机器人用无框电机市场规模预计达60亿元,2030年或突破280亿元,国产替代率有望从30%提升至50%。
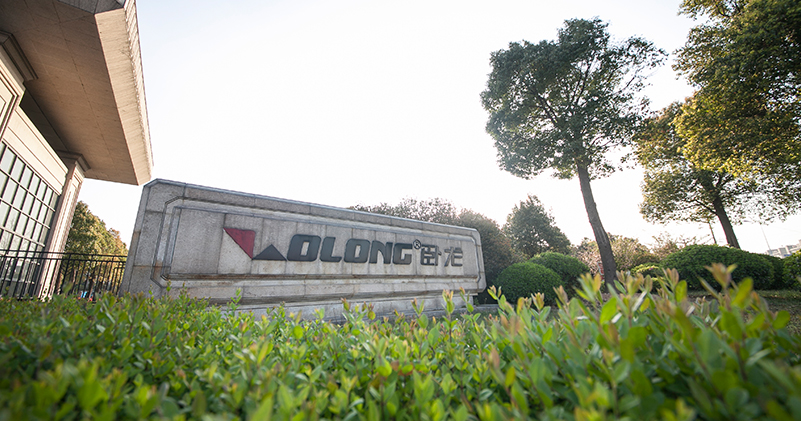
五、挑战与未来趋势
技术瓶颈:
高端产品转矩密度与可靠性仍落后外资品牌;
温升控制与定制化需求增加工艺复杂度。
创新方向:
双定子设计:如某专利方案通过内外定子布局提升抗冲击性,适配工业机器人高载荷需求
智能化集成:驱动器、编码器与电机一体化设计,减少信号干扰(如昊志机电的关节模组)
产业链协同:上游磁材企业与下游机器人厂商联合开发定制方案,加速场景落地
六,伺服一体轮:无框力矩电机的性能跃迁
我们的伺服一体轮作为无框力矩电机的集成化载体,将电机、驱动器、编码器与轮体深度融合,打造出“动力-控制-执行”三位一体的紧凑单元。其核心优势在于极致的空间利用率与爆发式动态响应——以80mm外径的典型设计为例,可输出150N·m峰值扭矩,承载100kg动态负载,却能省去传统减速器与传动结构,使AGV底盘或人形机器人关节的布局自由度提升40%以上。
无框力矩电机的低惯量特性让轮体响应时间压缩至2ms级别,无论是仓储机器人0.5米窄道内的±0.1mm精准停泊,还是人形机器人踝关节触地时的瞬时反向驱动,均可实现毫秒级力控交互。直接驱动技术进一步消除机械传动损耗,在同等负载下能耗降低15%-20%,配合IP65防护等级的一体化封装,即便在粉尘、油污或高频震动的工业场景中,仍能保障超20000小时无故障运行。
更关键的是,这类设计通过内置总线协议(如EtherCAT)支持多轮协同与力位混合控制。例如在爬坡越障时,系统可实时分配各轮扭矩,模拟生物肌群的协同发力;而在手术机器人等高敏场景中,其微米级定位精度与柔性输出特性,甚至能还原人类手指的操作触感。这种“硬件即算法载体”的特性,正重新定义机器人运动控制的边界。
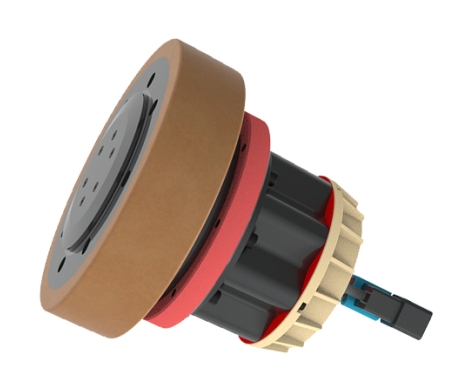
结语
无框力矩电机作为人形机器人的“肌肉系统”,其技术突破与制造升级直接关乎机器人性能天花板。尽管国产企业在工艺积累与高端市场仍存差距,但通过差异化创新(如微型化、高性价比)与产业链协同,正逐步打破外资垄断。未来,随着AI驱动的人形机器人量产浪潮,这一赛道或将迎来“爆发式增长周期”。
您好!请登录